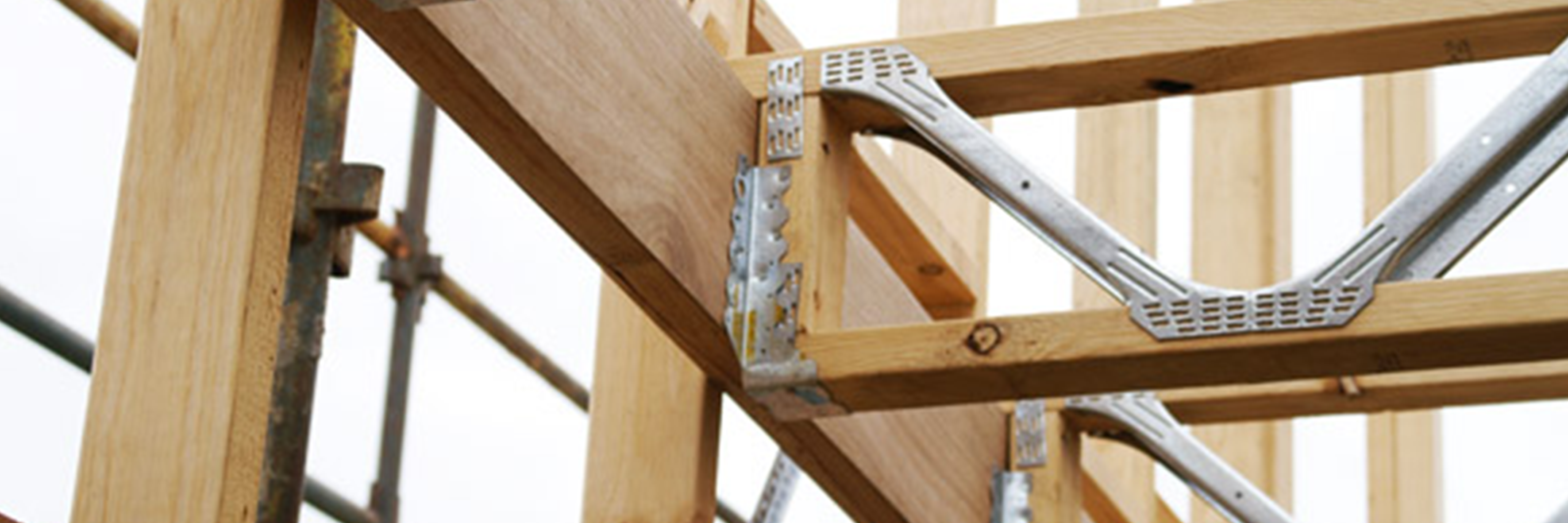
More and more developers and builders are looking for more cost-effective building products for both their large-scale residential...and commercial projects.
This scenario occurred on a ‘start-from-scratch’ school in the outer-suburbs of Melbourne - where the developer nearly had to return to the drawing board after an unexpected surge in the cost of steel.
‘I mainly work on larger commercial projects and had little knowledge of the capabilities of MiTek PosiStruts,’ said Andrew Waters, Project Manager with the ABI Group – part of the Axium Consortium overseeing the whole project. ‘We were working to very tight deadlines with the school due to take students within the next 12 months; so we had to get a solution...and get one fast!
We turned to our fabricator for a the answer.’ Bowens Roof Trusses were supplying all the prefabricated wall frames and welcomed the opportunity to tender for the prefabrication of the roof. ‘After further investigation, and some valuable input from the team at Bowens, it quickly became apparent PosiStruts would be ideal for the construction of the school roof,’ added Andrew. ‘The pressure would be on Bowens though as we had a lot of roof to build and not a lot of time to bring it all together.’
The co-ordination and communication between all parties was going to have to be something special to see this all come to fruition...on time.
The first of 5 large slabs of concrete was poured; with the wall frames hot on their heels. Then it was time for the PosiStruts...all 14,500 lineal meters of them,’said Jim Raso, Commercial Prefabrication Detailer at Bowens.
‘‘There were more than 2000 individual PosiStruts, incorporating over 35,000 lineal metres of timber, 45,000 + PosiStrut Webs...and nearly 40,000 Gang- Nail connector plates!’
The longest of the PosiStruts were in excess of 11m (doubled), with most of these accommodating a 1.2m cantilever.
Open space and free-flowing movement within the structures was a constant theme – hence the requirement for large spanned areas. Most PosiStruts were fixed via bottom chord support; however there were areas where top chord support proved more practical.
Steel isn’t just expensive. Steel adds weight and weight means extra, deeper footings – and that all adds even more cost!’
This scenario occurred on a ‘start-from-scratch’ school in the outer-suburbs of Melbourne - where the developer nearly had to return to the drawing board after an unexpected surge in the cost of steel.
‘I mainly work on larger commercial projects and had little knowledge of the capabilities of MiTek PosiStruts,’ said Andrew Waters, Project Manager with the ABI Group – part of the Axium Consortium overseeing the whole project. ‘We were working to very tight deadlines with the school due to take students within the next 12 months; so we had to get a solution...and get one fast!
We turned to our fabricator for a the answer.’ Bowens Roof Trusses were supplying all the prefabricated wall frames and welcomed the opportunity to tender for the prefabrication of the roof. ‘After further investigation, and some valuable input from the team at Bowens, it quickly became apparent PosiStruts would be ideal for the construction of the school roof,’ added Andrew. ‘The pressure would be on Bowens though as we had a lot of roof to build and not a lot of time to bring it all together.’
The co-ordination and communication between all parties was going to have to be something special to see this all come to fruition...on time.
The first of 5 large slabs of concrete was poured; with the wall frames hot on their heels. Then it was time for the PosiStruts...all 14,500 lineal meters of them,’said Jim Raso, Commercial Prefabrication Detailer at Bowens.
‘‘There were more than 2000 individual PosiStruts, incorporating over 35,000 lineal metres of timber, 45,000 + PosiStrut Webs...and nearly 40,000 Gang- Nail connector plates!’
The longest of the PosiStruts were in excess of 11m (doubled), with most of these accommodating a 1.2m cantilever.
Open space and free-flowing movement within the structures was a constant theme – hence the requirement for large spanned areas. Most PosiStruts were fixed via bottom chord support; however there were areas where top chord support proved more practical.
‘All-up, PosiStruts... were far and away the best solution for this job.
Not only did they answer our roofing needs, but they also continued to work for us on-site!“We could run electrical, plumbing and air conditioning ducts through the PosiStruts, all without having to drill holes or compromise on the structural integrity of the structure,’ added Andrew.
‘When you’re working with steel there’s very little room for error – and even less opportunity to ‘move’ things if changes on-site are required.Steel isn’t just expensive. Steel adds weight and weight means extra, deeper footings – and that all adds even more cost!’